Center for Hydrographic Studies, Madrid
Miguel Fisac- Type Commercial / Office Prefabrication Headquarters / office
- Material Concrete
- Date 1960 - 1963
- City Madrid
- Country Spain
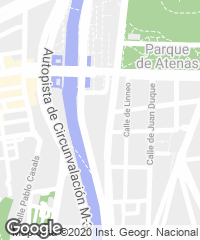
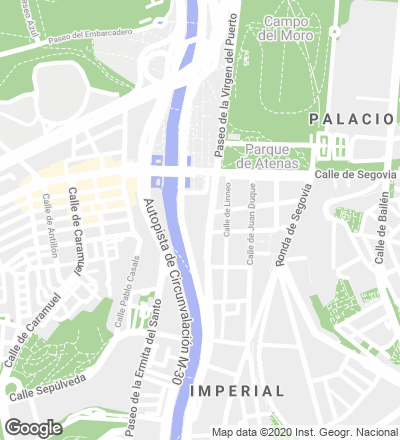
The reproach of his friend Fernando Casinello for his lack of interest towards the structural solutions in his projects encouraged Fisac to test, in the competition for the church of San Esteban in Cuenca (1960), double curvature beams whose section reveals basic features of the Center for Hydrographic Studies, the work that inaugurated his professional maturity.
“The program demanded a homogeneous illumination for the laboratory, and I thought that it was necessary to invent a mechanism to avoid direct sunlight. I studied the general sunning conditions and came to the conclusion that the roof should consist of consecutive sloped plans. I handed it over to José María Priego – an engineer they had for the construction of dams – and he told me that with a 22 meter span he could not build pre-stressed concrete beams because it was impossible to raise such large pieces. I thought about it over and over again until I came up with a solution of voussoirs that resembled a cow’s bone; I started to do some tests with the bone and the engineer found the center of gravity. So the structure consists of one-meter wide and almost two meter high elements that are linked up by the catenary of the post-stressed cables. But post-stressing is a difficult technique, and I needed the right person to do it; then I learned about Ricardo Barredo, who held a patent for poststressing anchorings and for the injection of the cable sheathing, which is the most difficult part. The beams were assembled by installing a trestle at the end height of the roof structure; once the elements had been placed on top of it, the cables were inserted in a metallic sheath, and then stretched from the ends until reaching the final stress. After installing the anchorings, finally the cement was injected to avoid the corrosion of the steel wires. This technically complex procedure can be avoided through pre-stressing, that consists simply of taking some previously stretched wires and then pouring the concrete, letting it set. As it is all finished when taken to the site, this method is safer and cheaper.”
“Nowadays, with cranes of over 400 tons, prestressing is a good choice, but to make prestressed beams of a certain size you need adequate means of transportation and elevation, which we did not have then. In this building, poststressing was chosen because it allowed to make the pieces more manageable; the beam consisted of a series of voussoirs built from a double formwork of metal sheet, concreted horizontally.”... [+]