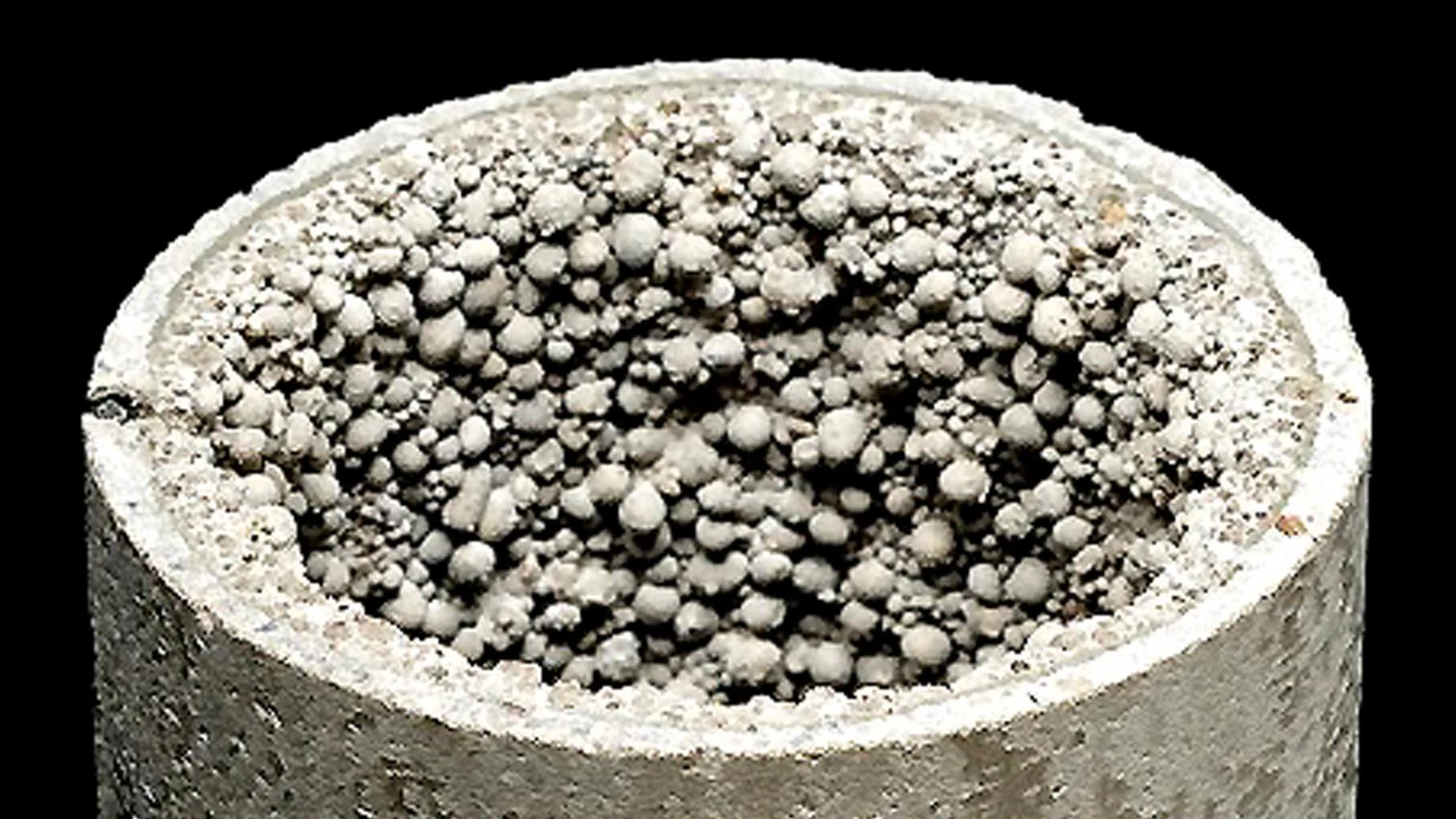
Since its very beginnings, the concrete industry has always gone hand in hand with the production of chemical agents that have the potential to improve the properties of the material. At first, the focus of these chemical products was on reducing the setting or hardening time of concrete, but research in this area soon turned to the problem of making concrete more watertight and damp-proof, and later to manufacturing plasticizers that would help to make mixtures more homogeneous in texture.
The improvement process continues. The invention and commercialization of cements of high mechanical resistance – which are widely applied in the construction of high-rise buildings – was soon followed by that of products which enhance the performance of concrete in reaction to traction or retraction. In constant development since the decade of the 1960s, such additives basically consist of fibers of different kinds – whether of polypropylene, metal, or silica micropowders – that are added to the cement during execution, with the aim of reducing fissures in the mixtures and thus also improving concrete’s overall mechanical resistance. A simple example will suffice to illustrate this: the mere addition of 0.9 kilograms of polypropylene fibers for every cubic meter of concrete is equivalent to 180,000 meters of conventional reinforcement steel frame.
But the innovations do not end there. After decontaminating concretes, ecological concretes, biological concretes, and translucent concretes (see Arquitectura Viva 136, 148, 152 and 154) came the appearance, just recently, of two new families of products: on one hand self-healing and flexible concretes (see Arquitectura Viva 152), and on the other hand concretes shaped with a gradient. While the former present properties resembling those of steel (they can deform to up to 5% of their initial sizes), the latter come from spatially distributing, as desired and through gentle transitions, different materials or degrees of porosity in a matrix of concrete. Coming from aeronautic technology, the idea will in the future make it possible to save on material as well as improve its performance, also increasing both its transmission capacity and its density. Therefore,it is probable that concretes in gradient will be applied in architectural enclosures made of a single material that is able to address all requirements, and perhaps supplied with 3D printers.