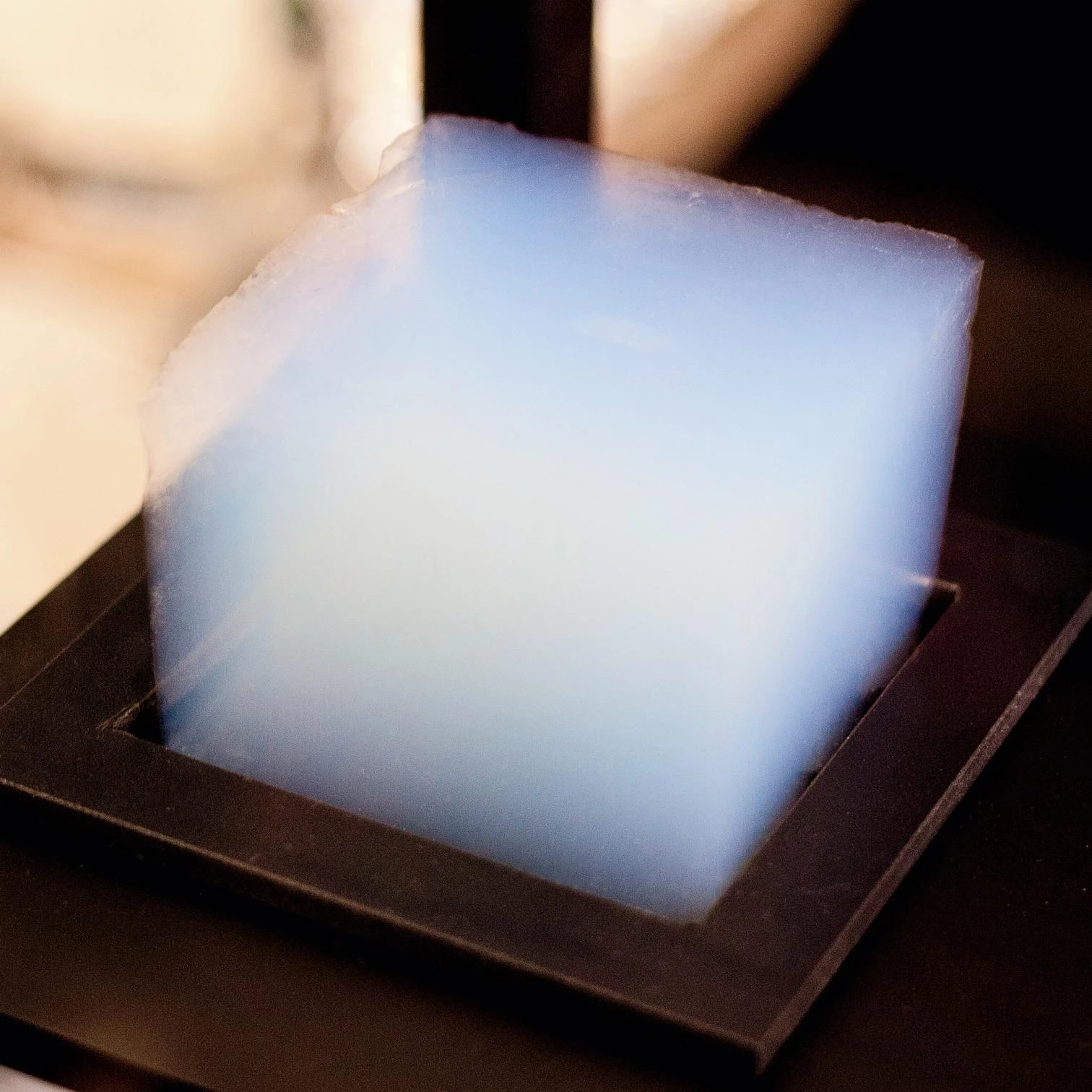
Like the discovery of so many other materials, the invention of aerogels came about through a bet, or better, through a streak of serendipity. In the year 1930, the chemical engineer Samuel Stephen Kistler was challenged by a friend to extract liquid from a jar of jam without diminishing its volume. Kistler hit upon a general way of replacing the liquid of a compound with gas, using different materials, such as silica, tin or aluminum, for a base. This was the origin of what would subsequently come to be known as ‘aerogel’, commonly known as ‘frozen smoke’ or ‘blue smoke’ because of its translucent appearance and color. As its name indicates, it is a gel, a colloidal (solid-liquid) substance that is 99.8% air, which explains the extreme lightness of aerogels: three times denser than air, but a thousand times less dense than common glass.
Because of their chemical constitution, aerogels are extremely resistant. They are able to withstand weights of over a thousand times their own. Also, although they are transparent, they have a very low thermal transmission coefficient. Furthermore, aerogels can be laminated into very fine sheets. Because of this, their potential for technological application is very broad. They can be used as super-insulating material in special clothing and as thermal protection in airplanes or capsules. They can even be used as shock absorber in automobiles, thanks to their capacity to curb the intensity of collisions by as much as 89%.
Developed several decades ago, the traditional aerogels are made of silica foam, which brings its price down considerably – silica is extracted from common sand –, although consistency is affected because silica makes them fragile and breakable. This explains why, for architectural applications, aerogels come in the form of nano-aerogels (not to be confused with the nanogels of cellular biology) formed by particles used as filling in transparent or translucent panels of more conventional materials, such as cellular polycarbonate, polyester resin or glass, giving rise, for example, to the well-known products that are commercialized by Cabot (panels with a U of up to 0.54 E/m2K, which means a 1 W/m2K reduction with respect to a conventional panel of the same thickness) or Roda (multilayered polycarbonate panels with a U of 0.48 W/m2K for a thickness of 5 centimeters).
When combined with these materials, silica foam ceases to be fragile, without in the process losing its thermal properties. This serves to improve the insulation capacity of building enclosures, for example, reducing thickness substantially (1 centimeter of aerogel is a little more than 3.5 centimeters of fiberglass) and ultimately allowing the transparency and lightness that is held as the ideal in a good part of contemporary architecture.
Nevertheless, the costs incurred by these solutions and the limitations that come to the fore when they are applied have led to the undertaking of new investigations aimed at reducing the essential fragility of aerogels, this by altering their molecular make-up through the incorporation of either conventional polymers or polyamides, which strengthen the silica networks that stretch through the aerogel’s structure.