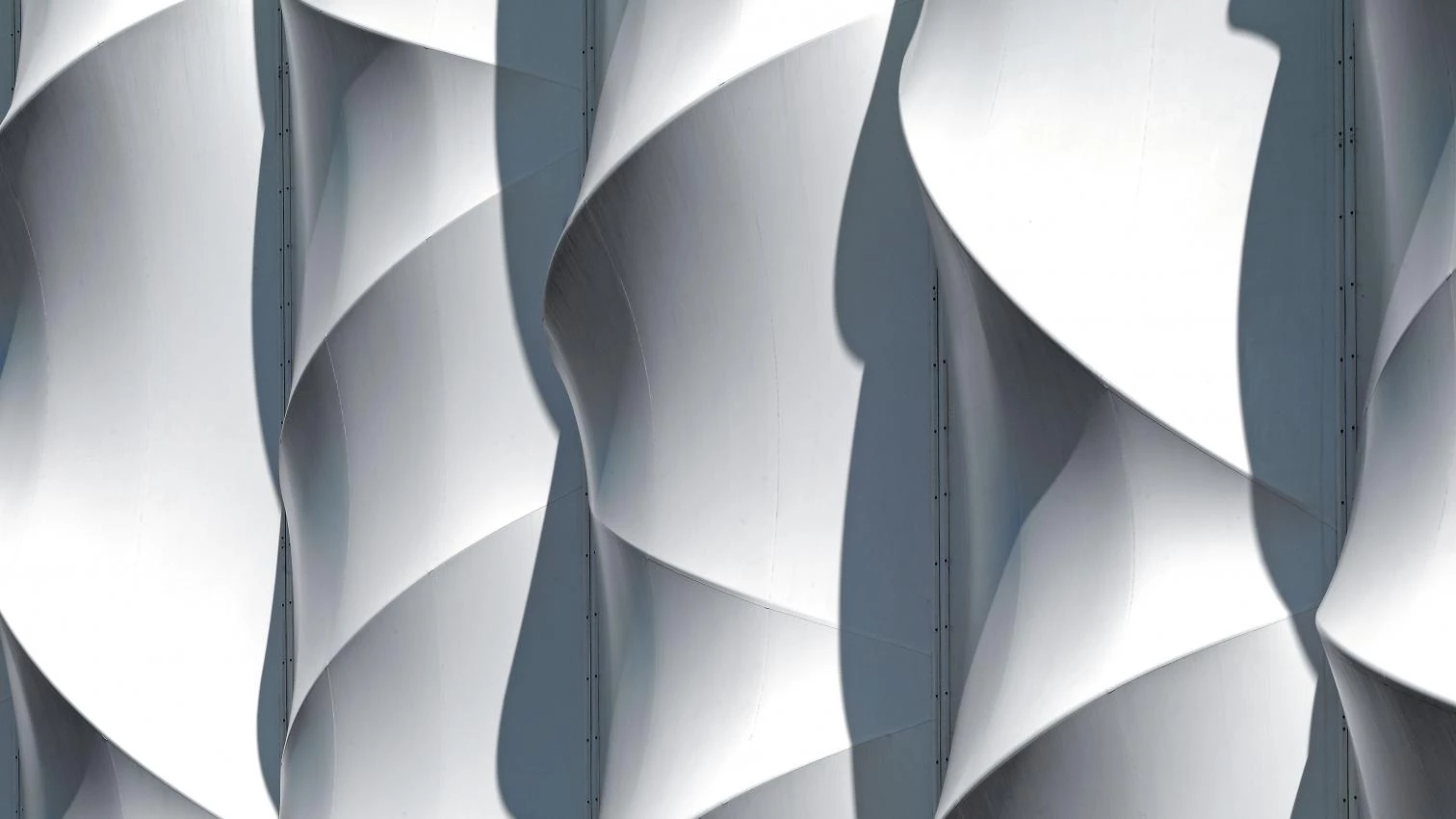
How much does your building weigh? A quick calculation suffices to see that in general, buildings weigh too much. Lightness is no trivial matter if resources are limited, and a very efficient strategy from the viewpoint of sustainability is to design light buildings.
A conventional metal structure of the kind considered ‘light’ can bring down weight to 30 kilograms of structure per square meter covered. Textile architecture offers a more sustainable answer: for example, a structure of stressed cables to stabilize floating uprights by tensegrity (islands of floating compression in a sea of traction), combined with a structural membrane, can drop to 10 kilograms per square meter covered. The membranes also make for effective solar protection and energy saving besides natural lighting of interiors, without need for electricity, and they are durable and recyclable (when the London Olympics ended, all textile constructions raised for the event were dismantled and either relocated or recycled).
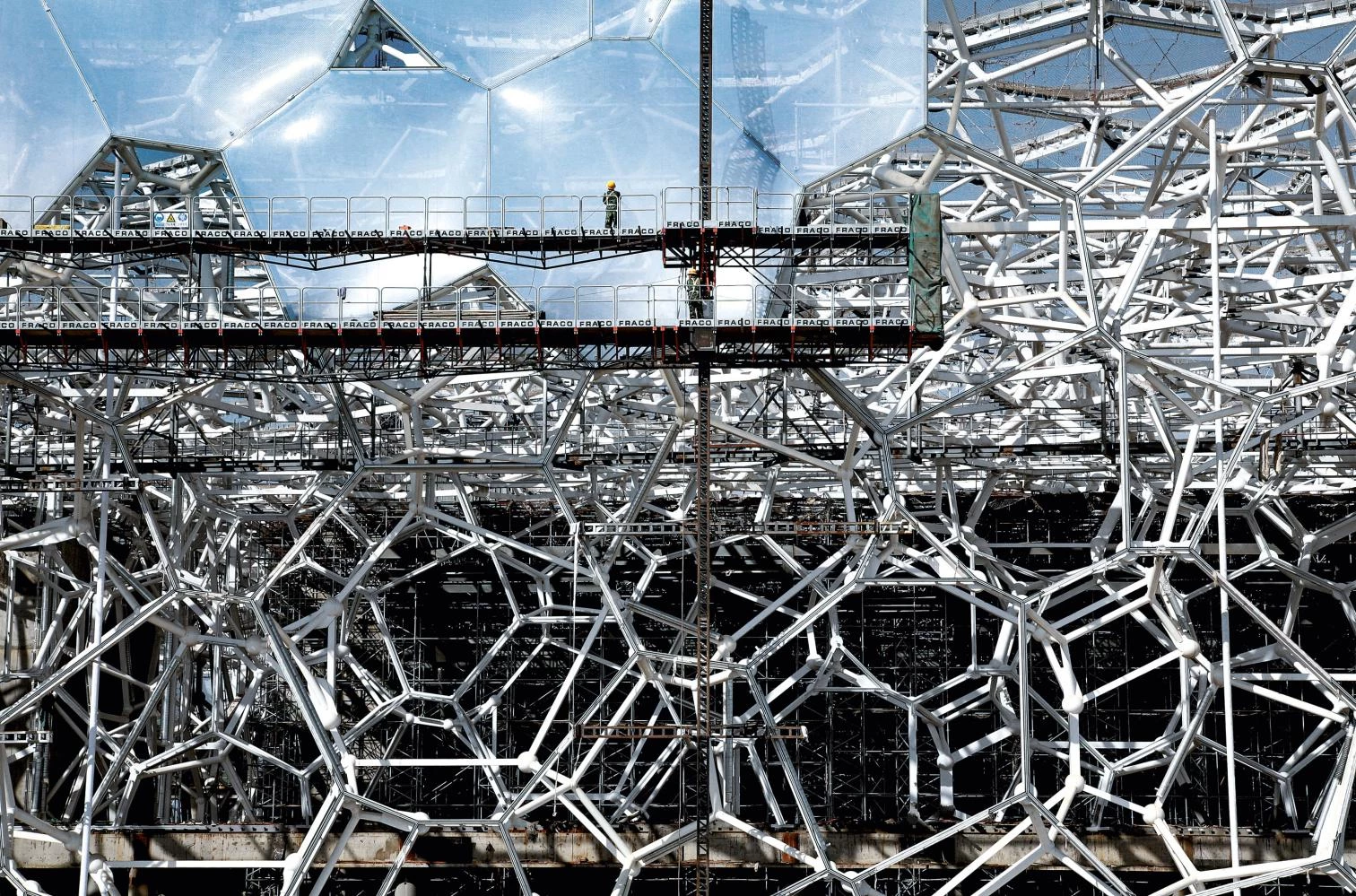
Building with membranes is as old as the need of nomadic people to transport shelters that were light and easy to set up. This requirement gave fabrics the function of protecting inhabitable spaces, and they were generally held up by very primitive structures made of wooden posts and ropes. The tepees of North American Indians, Mongolian yurts, and the Berber haima are good examples. Later, the wood and ropes gave way to steel uprights and cables, and the high-traction roofs of Shukhov, Severud, or Nowicki (Raleigh Arena), as well as circus tents from the 19th century on, continued the development of this light architecture.
Equilibrium, Curvature, Prestress
The use of textile materials does not necessarily mean we are talking about ‘textile architecture.’ Tepees and yurts, the velarium over the Colosseum grandstand, canvas tents at fairs, and canopies protecting shopping streets are roofs made of cloth materials, but they do not count as textile architecture because the fabric performs no structural function. The haimas of Arabian nomads are structural. For a membrane to be structural, and therefore resistant to external actions (mainly wind), two conditions must be met: a curved form, resistant to deformations; and stabilization thereof through prestressing of the fabric in its two main directions (warp and weft).
Frei Otto is considered the father of textile architecture as it was he who laid down its design and calculation bases. Although textile materials were not used in his early works (including the German Pavilion at the Montreal Expo and the Munich Olympic Arena), or if they were, only as enclosure, not structure, the cable nets that materialized the geometries already met the requirements of form and prestress.
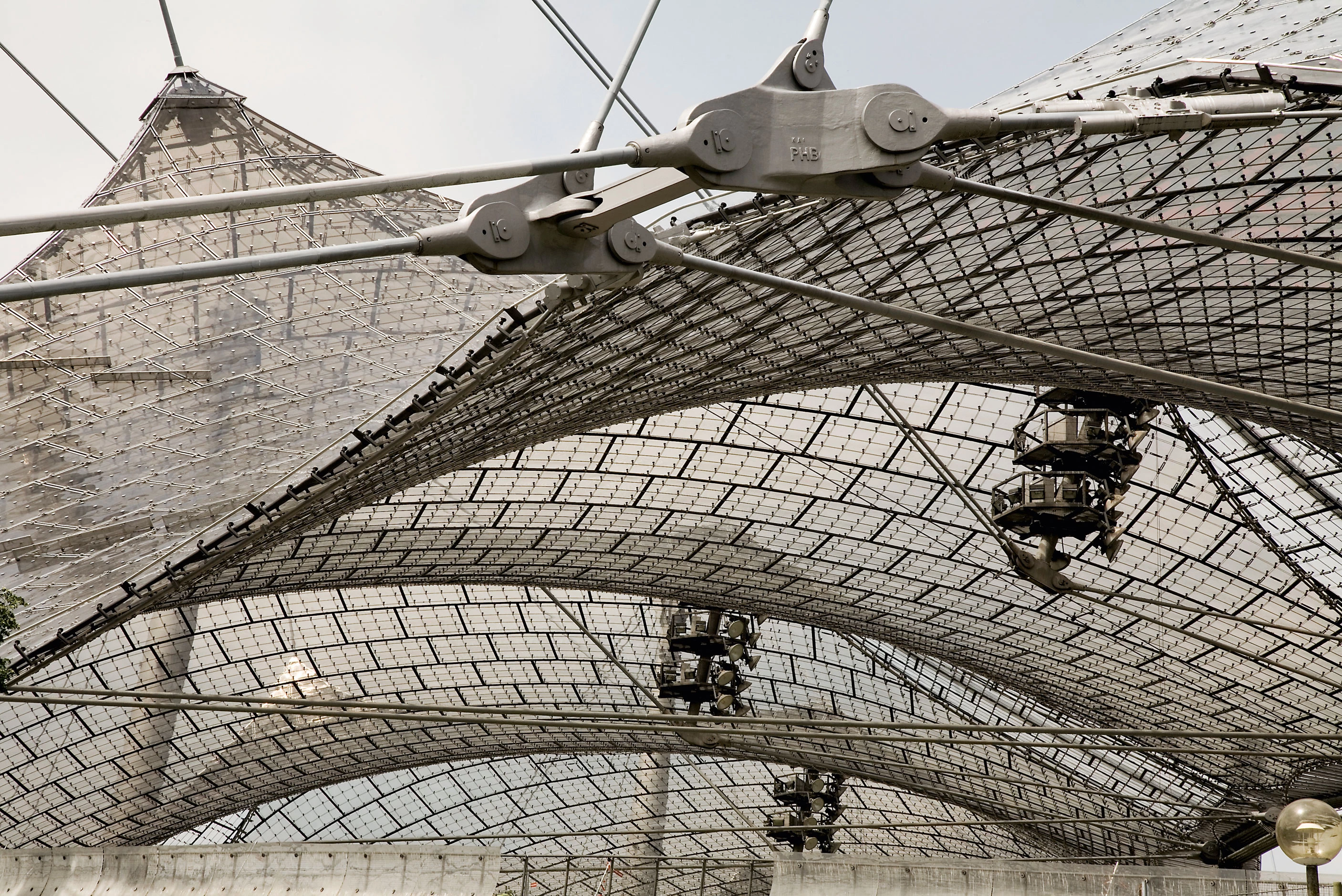
Later, tensostatic roofs would use resistant and durable structural membranes, further lightening constructions by limiting the structure to the edges of the membrane (cables, uprights, arches), coming down to our days of projects with huge spans (stadiums, airports, stations, commercial centers) and structural enclosures consisting in a tensile membrane. The geometry of these tensostatic roofs (with a double curvature in opposite directions at each point, or anticlastic), along with the prestress force introduced into the membrane, gives it resistance. This is because the opposed curves take turns in absorbing compression forces (wind, snow, maintenance) or the suction caused by wind. In this way, and because the radius of curvature and the tension in the membrane are proportional, for a balanced roof, the greater the curvature of the membrane, the less prestress force is needed. So, the greater the curvature of a roof, the stabler it is.
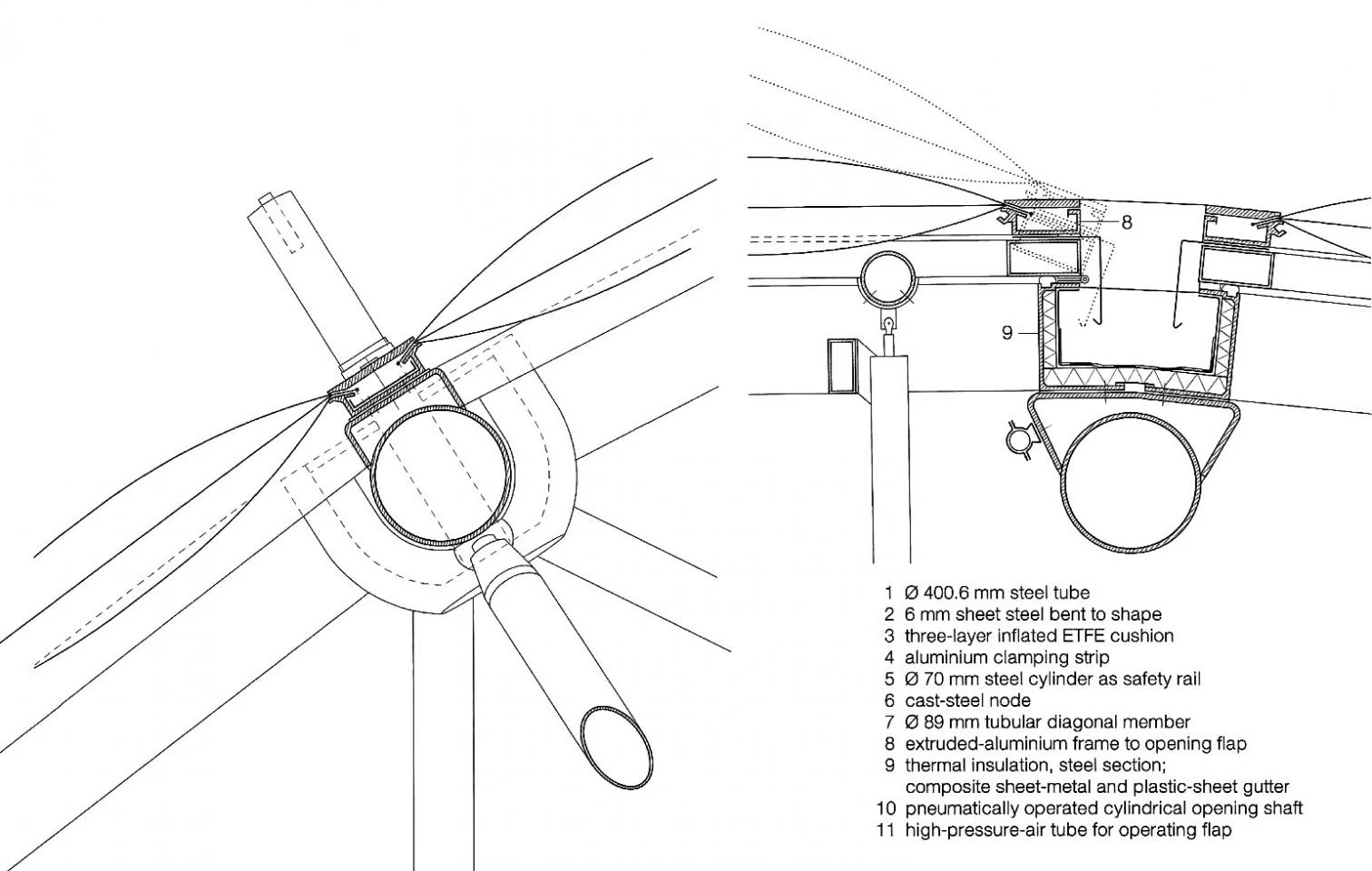
Los textiles suelen emplearse en cubiertas tensadas anticlásticas, de doble curvatura en sentido opuesto, o bien en cubiertas sinclásticas infladas, de materiales como el ETFE, que se estabilizan mediante la presión del aire interior.
For this reason, and because there is only one optimal shape for equilibrium, we can say that, contrary to what it seems, in textile architecture form is not a free choice, or at least optimal form is not. This is not obtained from arbitrary design, nor by modeling surfaces with a conventional computer program. A special software is needed, one which considers the form of the membrane in equilibrium, with and without external loads.
For its part, in presostatic (inflated) roofs, the sinclastic (unidirectional at each point) curvature is stabilized by means of the pressure of air inside the roof, as in Anish Kapoor’s Leviathan in Paris. Roofs of this kind (see Arquitectura Viva 163) require less structure (because the structure is in fact the membrane and the pressurized inner air), but they need more maintenance because in spaces of great volume, internal pressure has to be kept up. So this typology has begun to give way to roofs made of cushions, where compressed air is confined in smaller cushions, as in Herzog & de Meuron’s Allianz Arena in Munich, where a rhomboidal grid shapes the facade and roof with close to 3,000 ETFE foil cushions.
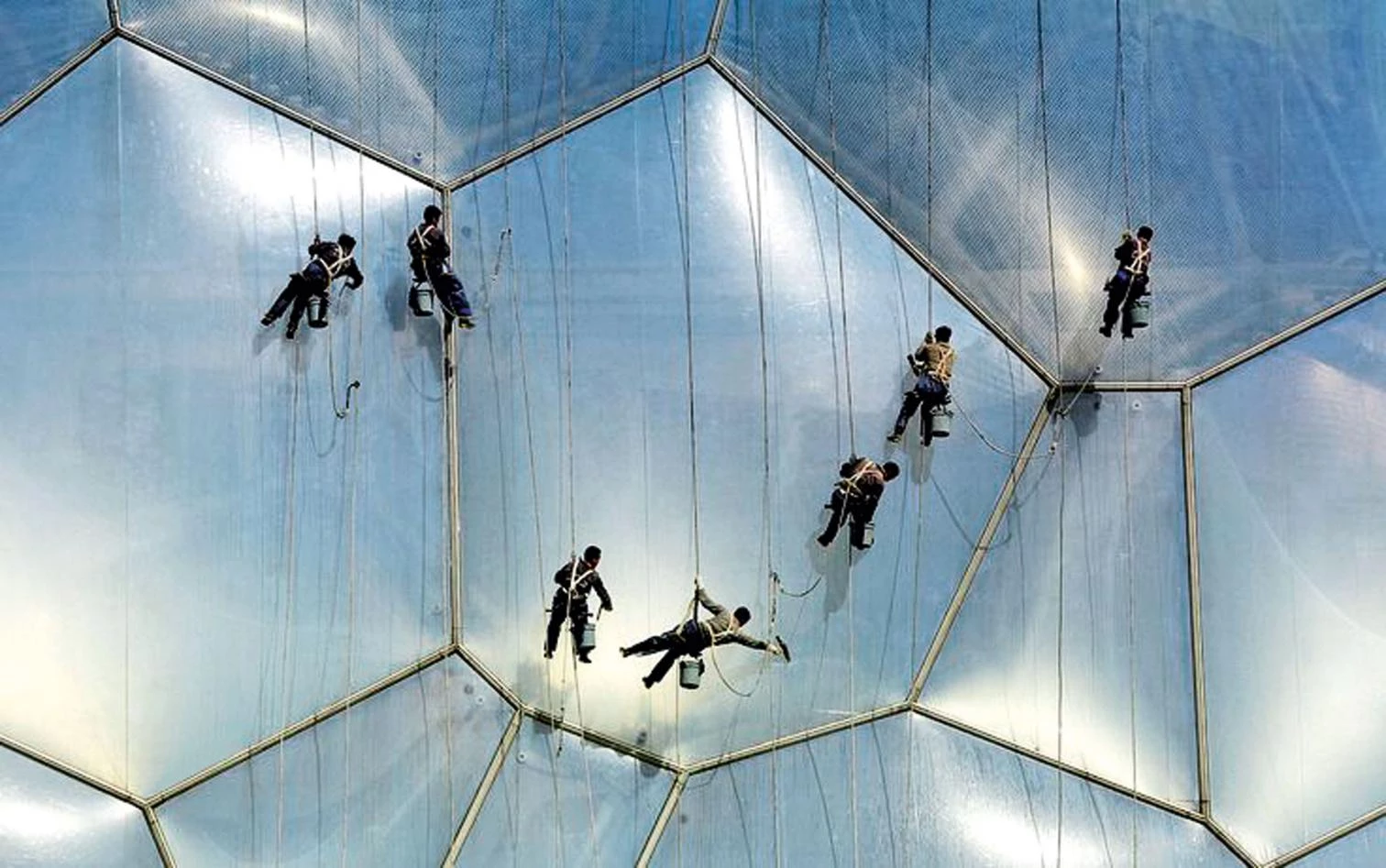
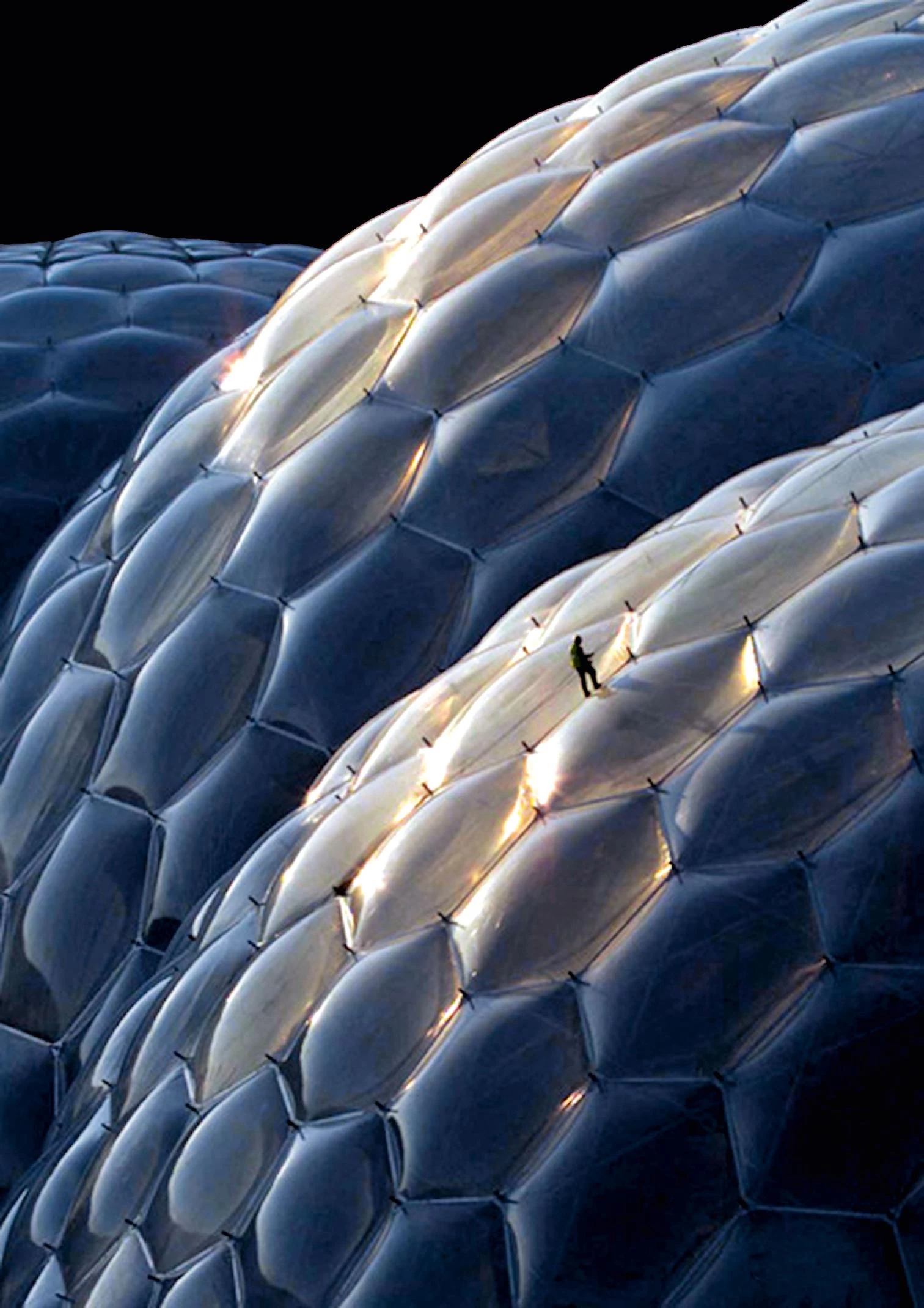
New Materials
Textile architecture is built with materials of minimal thickness. In the case of ETFE, with foils of a single material en masse, calendered to thicknesses of tenths of a millimeter. Thanks to its transparency qualities (up to 95%), ethylene tetrafluoroethylene has properties which are useful for enclosing spaces where amounts of radiation are required, as in the first major work to be carried out with this material, Grimshaw’s Eden Project in Cornwall (UK).
In the case of composite membranes, an inner fabric made with high-tenacity polyester, fiberglass, or PTFE yarns provides resistance to traction, while a plastic cladding of polymers (PVC, PTFE, silicone, etc.) protects the fabric and makes it possible for the roof patterns to be carried out by welding.
In development of late are products with improved properties and durability, with finishes which have greater resistance to external agents. This is the case of the fluoride composites in three-dimensional grids integrated into the membrane itself, like Ferrari’s TX30, which boasts a life of over thirty years, or Taiyo’s titanium dioxide (TiO2) varnish, used in the roof of Shigeru Ban’s Centre Pompidou in Metz. This finish also generates a photocatalytic reaction that decomposes the greenhouse effect gases (NOx).
Another growing tendency in textile architecture is the quest for greater transparency. In this sense, the ETFE sheet is far unrivaled, but because it has no inner fabric that prevents deformations, use of it requires reinforcement with cables or the construction of small pneumatic cushions. To achieve transparency with a single layer of fabric without reinforcements, new membranes have been developed which are made of fiberglass fabric and ETFE foil cladding, like Ferrari’s Flexlight FX701, which allows 65% of light in.
Other innovations have centered on improving capacity for thermal or acoustic insulation. In this sense, new materials like aerogel have been incorporated into double- or triple-layer composite membranes to obtain higher degrees of thermal insulation than in conventional materials, but with less thickness and maintaining a certain translucence.
Microperforated meshes, improved and adapted to exterior use, are also now being incorporated into facades. Its use as solar protection, whether in collapsible canopies or blinds, or as textiles fixed on facades, much reduces energy consumption in air conditioning and gives visual comfort as well. These attributes have generated a new system for ventilated facades, the textile facade, as in Josep Miàs’s new Iguzzini center in Barcelona, where the mesh is stretched against the structure of the facade.
Finally, certain microperforated meshes incorporate lighting through the interweaving of optic fiber, as in C. Sainz and J. Tejera’s Batylux patent for Ferrari, used for the first time in the District Heating project of Federico Soriano in Madrid. Other projects, such as Ackermann & Partners’ AWM Carport in Munich, have started a line of development of textile architecture, based on the incorporation of flexible photovoltaic cells on light textile supports. Textile architecture is currently developing along two lines: through the creation of new materials with ever more sophisticated properties; and through the quest for structural weightlessness for the sake of truly sustainable construction.
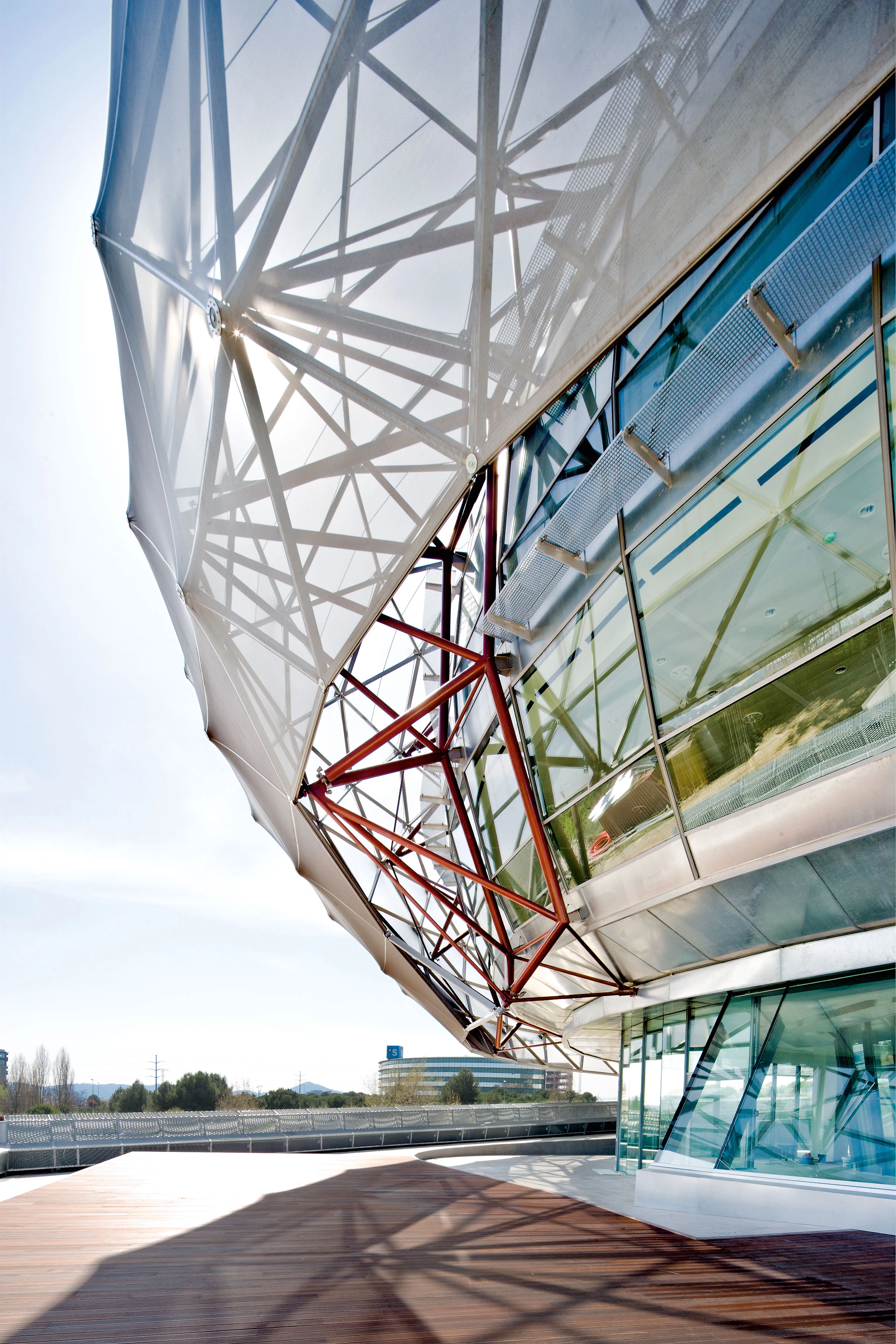